Firmen im Artikel
Inhaltsverzeichnis
1. Die Umsetzung des Internets der Dinge (IoT)
2. Datendurchgängigkeit als wünschenswertes Ziel
3. Die Rolle von OPC UA in der Industrie 4.0
4. Plattformen und Ökosysteme
5. Wie steigt man am besten in die Digitalisierung ein?
6. Bestandsanlagen ins IoT bringen
elektro AUTOMATION: Wo steht die produzierende deutsche Industrie auf dem Weg in die Industrie 4.0? Sind wir schon so weit, wie wir sein könnten?
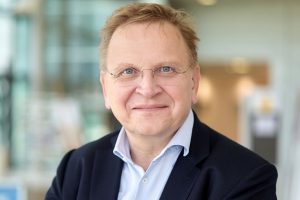
Bild: Open Industry 4.0 Alliance
Nils Herzberg (Sprecher des Vorstands der Open Industry 4.0 Alliance & Global Head Strategic Partnerships for Digital Supply Chain and Industry 4.0 bei SAP): Industrie 4.0 wurde als eine Revolution vor 10 Jahren angekündigt, jedoch hat sie sich als Evolution entpuppt. Wenn man diese 10-jährige Evolution betrachtet, wird der große Quantensprung deutlich. Offensichtlich ist, dass die Vorteile von Industrie-4.0-Konzepten in neueren Fabriken, Anlagen oder Logistikzentren zu sehen sind. Es gibt jedoch auch immer noch Herausforderungen – so würde beispielsweise das neue Datengesetz aus Brüssel die Industrie vor eine nächste Welle relevanter Herausforderungen stellen.
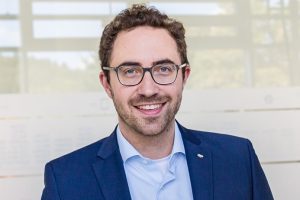
Bild: Open Industry 4.0 Alliance
Marius Grathwohl (Chairman Industry Focused Workgroups der Open Industry 4.0 Alliance und Vice President Digital Products and Transformation bei der Multivac Group): Wir befinden uns aus meiner Sicht in einer Phase der Exploration und Pilotierung. Cyber-physische Systeme sind noch nicht breit im Einsatz, doch es werden die Grundlagen dafür geschaffen. Maschinen werden mit der für Konnektivität notwendigen Infrastruktur ausgestattet und vielfach sind sie auch schon Teil des Industrial Internet of Things (IIoT). Erstaunlich viele Firmen sind derzeit aber noch damit beschäftigt, traditionelle IT-Anbindungen des Shopfloors zu realisieren und zum Beispiel MES- und SCADA-Systeme auszurollen, da für den Einsatz dieser Systeme bereits zahlreiche Referenzen existieren. Gerade kleine und mittlere Firmen, die den initialen Invest in klassische On-Premise-Systeme scheuen, erproben allerdings meiner Erfahrung nach die neuen Wege in die Cloud.
Die Umsetzung des Internets der Dinge (IoT)
elektro AUTOMATION: Ist der deutsche Maschinenbau denn schon im IoT oder IIoT angekommen?
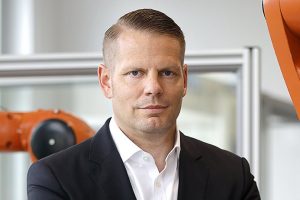
Bild: Open Industry 4.0 Alliance
Dr. Christian Liedtke (Chairman Membership & Sales bei der Open Industry 4.0 Alliance und Head of Strategic Alliances bei Kuka): Sagen wir es mal so – der Digitalisierungszug kommt nur langsam in Fahrt. Es gibt viele Lösungen, aber keine Interoperabilität – also keine Fähigkeit, das Zusammenspiel unterschiedlicher Maschinen und Komponenten unter Einhaltung gemeinsamer technischer Standards auf die Schiene zu bringen. Viele Unternehmen finden sich mit der derzeitigen Situation ab. Die Prozesse laufen ok, sind in vielen Branchen vor allem mit Blick auf Europa, schon sehr gut ausgereift. Aber erste Pilotanwendungen haben oft nur marginale Verbesserungen aufgezeigt. Es braucht prozess- und fabrikübergreifende Lösungen, die das IoT gesamtheitlich betrachten. Nur so können sich Mehrwerte entwickeln. Individuelle Verbesserungen können Engpässe nur von einer Maschine zur nächsten verschieben. Eine Verbesserung der gesamten Produktion muss mit einem herstellerübergreifenden Austausch von Daten einhergehen. Hier gibt es durchaus noch Potenzial.
Datendurchgängigkeit als wünschenswertes Ziel
elektro AUTOMATION: Wie lässt sich dieser herstellerübergreifende Austausch von Daten denn erreichen?
Liedtke: Durch die schnellen technologischen Weiterentwicklungen sind einzelne Unternehmen – egal wie groß sie sind – nicht in der Lage, die Digitalisierung allein zu stemmen. Genau hier setzt deswegen ja der Gedanke der Open Industry 4.0 Alliance an. Als Umsetzungsallianz stellen wir sicher, dass sich die Mitgliedsunternehmen an einen Tisch setzen, um gemeinsam an einer übergreifenden Lösung zu arbeiten. Wir wollen, dass der Digitalisierungszug an Fahrt aufnimmt – und das eher als ICE. Deswegen setzen wir in der Allianz auf Offenheit. Die geht sogar so weit, dass Unternehmen noch nicht einmal Mitglied sein müssen, aber trotzdem auf den fahrenden Zug aufspringen und mitfahren können. Fest steht: Silodenken muss der Vergangenheit angehören.
„Noch wird die wirkliche Power der Edge überhaupt nicht genutzt“
elektro AUTOMATION: Wie lassen sich die Datensilos aufbrechen, wie verhindert man den ‚Daten-Protektionismus‘?
Liedtke: Es braucht den Mut der Kunden, um Unternehmen zu vertrauen. Es braucht zusätzlich Pioniere, die den Vorstoß wagen und darauf vertrauen, dass Licht am Ende des Tunnels ist und uns kein Zug im Tunnel entgegenkommt. Die Allianz vereint dazu unterschiedlichste Unternehmen, um die realen oder fiktiven Probleme zu lösen; um das Vertrauen der Kunden zu gewinnen. So entsteht ein Mehrwert der Zusammenarbeit. Gelingt uns – als Allianz – das anhand einfacher Use-Cases, können wir den nächsten Schritt machen. Der umfasst, dass wir uns an Wertschöpfungsnetzwerke herantrauen, um damit die Potentiale tatsächlich zu realisieren, von denen man seit mehr als 10 Jahren Industrie 4.0 träumt.
Die Rolle von OPC UA in der Industrie 4.0
elektro AUTOMATION: Nun sind Standards gerade im Bereich der M2M-Kommunikation ja nichts grundlegend Neues – kann den speziell OPC UA nicht heute schon wesentlich mehr im Sinne einer ‚Plug&play-Vernetzung‘ bieten?
Herzberg: Die Schaffung der sogenannten ‚Companion Specs‘ in Zusammenarbeit mit den Maschinenherstellern war und ist ein guter und zukunftsweisender Schritt in die richtige Richtung. Auch die ‚Unified Architecture‘ war zu ihrer Zeit eine gute Sache. Allerdings muss beachtet werden: Architekturen verändern sich im Eiltempo. Hier müssen die Standardisierungs-Organisationen zwingend Schritt halten. Entscheidend für den Erfolg von Industrie 4.0 ist die Umsetzung der Standards in den Maschinen und der Software – entscheidend ist nicht die Existenz der Standards an sich. Genau hier kommt wiederum die Open Industry 4.0 Alliance ins Spiel. OI4 hat sich die kohärente Umsetzung einer Gruppe von Standards auf die Fahne geschrieben. Wir wollen insbesondere unseren Mitgliedern – aber auch der Allgemeinheit –, Implementierungshinweise zu dem kohärenten Umgang mit Standards rund um Industrial Security, Datensicherheit, Souveränität oder Semantik geben. Dabei geht es uns nicht nur um technische Daten, sondern auch um Informationen wie Stammdaten, Dokumentdaten wie Reparaturanweisungen oder Ersatzteilbevorratung und natürlich um IIoT-Daten.
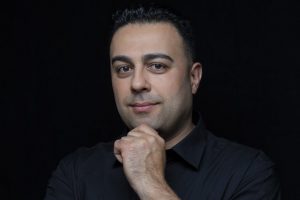
Bild: Open Industry 4.0 Alliance
Ekrem Yigitdoel (Managing Director der Open Industry 4.0 Alliance): Aus meiner Sicht sind die heutigen Standards noch nicht vollumfänglich in der Breite angekommen. Es bedarf einer Architektur, die es erlaubt, an der entsprechenden Stelle die Interoperabilität zunächst bereitzustellen, um diese anschließend für einen Datenaustausch nutzbar zu machen. Um das zu erreichen, müssen Leitplanken über Standards hinaus definiert sein, die es erlauben, die IIoT-Architekturen über eben diese implementierten Standards und verfügbar gemachten Daten zum Leben zu erwecken. Die Skalierung wird nur dann funktionieren, wenn beispielsweise die gesammelten Daten in einer vorgedachten Struktur abgelegt sind und auf diese je nach Use-Case und Zugriffsberechtigung einfach zugegriffen werden kann.
Plattformen und Ökosysteme
elektro AUTOMATION: Wie passen denn Ihre Vorstellungen zusammen etwa mit Cloud-Ökoystemen von BMW/Microsoft (Open Manufacturing Platform – OMP) oder VW/AWS (Industrial Cloud)?
Herzberg: Es steht uns nicht zu, die Initiativen unserer Mitglieder, oder unserer potentiellen Mitglieder im Detail zu kommentieren oder zu bewerten. Jedoch sehen wir in der Arbeit von BMW mit Microsoft oder VW mit AWS eine Bestätigung unserer Hypothesen. Letztlich sind bei beiden Initiativen die Umrisse einer Operator Cloud á la OI4 zu erkennen. Bei der Industrial Cloud gibt es wohl auch Ansätze bezüglich der Operator Edge. OMP hat sich außerdem der Schaffung von Open-Source-Lösungen verschrieben.
Yigitdoel: Rein technisch passen die Architekturen gut zusammen. Die OI4-Referenzarchitektur basiert auf dem RAMI-4.0-Modell und ist so gestaltet, dass die verschiedenen Technologieschichten sowohl vertikal als auch horizontal Daten bereitstellen, empfangen und damit verarbeiten können. Inwieweit die Bereitschaft der genannten Cloud-Ökosysteme existiert, diese von OI4 genutzten sicheren, aber offenen und interoperablen Konnektoren – wir nennen das in der OI4 ‚Points of Interoperability‘ – auszustatten, kann ich nicht beurteilen. Letztlich muss jedes Unternehmen den Mehrwert über die Technik hinaus für sich selbst definieren. Die wesentliche Frage lautet: Welche Vorteile verschaffe ich meinem Unternehmen und welche Anforderungen decke ich ab, wenn ich beispielsweise OI4-kompatible Technologien in meinem Cloud-Ökosystem nutze.
elektro AUTOMATION: Besteht dann nicht die Gefahr, dass getrennte Welten entstehen, zwischen denen übersetzt werden muss? Bietet sich nicht gerade hier OPC UA als Brücke an?
Herzberg: Sofern die Initiativen Standards wie die Verwaltungsschale, aber auch die Companion Specifications, umsetzen und offene – also dokumentierte und stabile – Schnittstellen bereitstellen, kann es interoperable und kompatible Welten geben. Da liefert die OPC Foundation – aber auch andere Standard-Organisationen – einige gute Ansätze. Jedoch werden wir trotzdem nicht völlig ohne Übersetzer auskommen. Mit einem leichten Augenzwinkern sei bemerkt: In der deutschen Sprache werden auch viele ‚Akzente‘ gesprochen.
Außerdem braucht es mehr gemeinsame Ansätze und Antworten rund um Datensicherheit und Datenmanagement, zur Semantik, zum Umgang mit Dokumenten und vieles andere mehr. Ein Blick auf die Catena-X-Initiative speziell für die automobile Wertschöpfungskette zeigt klar einen möglichen Weg in die interoperable und kompatible Zukunft – leider aber nur für ein Getriebe oder die Lichtmaschine, aber noch nicht für die Werkzeugmaschine, die mechatronische Komponente oder die Software zur Automatisierung von Geschäftsprozessen und Fabriken. Die Open Industry 4.0 Alliance würde einen ähnlichen Ansatz wie Catena-X für die gesamte Ausrüsterbranche – also Komponentenhersteller, Maschinenbauer, Automatisierer und IT-Provider sehr begrüßen.
Yigitdoel: Wir leben in der OI4 von der Vielfalt unserer Mitglieder. Es häng nicht allein von OPC UA ab, ob die Datendurchgängigkeit sowie Datenintegrität durchgängig erreicht wird. Da spielen weitere Faktoren hinein. Auf den Cloud-Layern sind andere Standards und Technologien im Einsatz. Die getrennten Welten können durch Initiativen wie die Open Industry 4.0 Alliance und Catena-X oder auch die Industrial Digital Twin Association (IDTA) überbückt werden. Über Implementierungsprojekte für Use-Cases und Problemstellungen in der Industrie können Lösungsansätze und die Nutzung vorhandener Standards gemeinsam erreicht werden.
Wie steigt man am besten in die Digitalisierung ein?
elektro AUTOMATION: Dann lassen Sie uns gerne auf einen praktischen Aspekt eingehen – wie sollte man in das Thema Digitalisierung einsteigen?

Bild: Open Industry 4.0 Alliance
Dr. Andrea Rösinger (Co-CEO und Chief Technology Officer Forcam): Unternehmen sind gut beraten, wenn sie die digitale Transformation der Fabrik in kleinen überschaubaren Schritten planen und zunächst mit einem Pilotprojekt starten. So kann die Hauptproduktion ungestört weiterlaufen und die Teams können Erfahrungen sammeln. Gleichzeitig sollte ein bereichsübergreifendes Change-Team den Gesamtprozess von Anfang an gemeinsam planen. Es sollte den späteren Rollout ebenso vorausdenken wie die Integrationsfähigkeit der IT-Architektur für künftige Anwendungen, zum Beispiel Künstliche Intelligenz (KI). Eine solche Composability ermöglichen modular nutzbare Systeme. Die wichtigsten technologischen Etappen einer erfolgreichen digitalen Reise lauten, unterschiedlichste Maschinen digital anzubinden, Big Data in Echtzeit in Smart Data zu wandeln und vorhandene wie neue Systeme nahtlos integrieren und komponieren zu können.
Erfolgreiche Industrie-4.0-Projekte zeichnen sich übrigens vor allem durch eine offene und vitale Führungs- und Kommunikationskultur 4.0 aus. Will heißen: Auf allen Ebenen erklären die Führungskräfte Ziele und Maßnahmen umfänglich, fangen Kritik und Sorgen auf, beziehen Know-how und Ideen von der Belegschaft mit ein.
elektro AUTOMATION: Was sind vielversprechende Anwendungen bei der Digitalisierung der Produktion? Wo sieht man am schnellsten erste Erfolge?

Bild: Open Industry 4.0 Alliance
Ricardo Dunkel (Technical Director der Open Industry 4.0 Alliance): Die Mehrwerte hängen stark von den einzelnen Unternehmen ab. Was wir in den letzten 2 Jahren jedoch alle beobachten konnten ist, dass der Vor-Ort-Einsatz etwa von Servicepersonal situationsbedingt stark zurück gegangen ist. Damit dies möglich wird, steht primär die Erfassung von Daten vor Ort und die anschließende Distribution in die vielfältigen Zielsysteme im Vordergrund. Ist diese Basis und eine sichere Konnektivität vorhanden, kann auf solche Situationen viel besser eingegangen werden, ohne dass Wartungs-, Produktions- oder Serviceprozesse darunter leiden.
Rösinger: Schnelle Erfolge sind abhängig von den Zielen jedes einzelnen Unternehmens. Meist geht es um größere Transparenz, höhere Effizienz und eine nachhaltige Innovationsfähigkeit der Fertigung. Performante IIoT-Lösungen bieten die Schlüssel dafür, durch umfassende Maschinen-Konnektivität, durch ein semantisches Datenmodell, den Digitalen Zwilling, durch Interoperabilität aller benötigten Systeme. Für kleinere Unternehmen versprechen dabei cloudbasierte SaaS-Lösungen – also Software as a Service – schnelle Effizienzerfolge. Dabei wird eine Softwarelösung in der Cloud mit den Signalen aus der Produktion gefüttert und diese werden in Smart Data umgewandelt, welche als nutzerfreundliche Analysen auf den Terminals der Werker erscheinen. Für mittlere und größere Unternehmen mit internationalen Produktionsstandorten eignen sich modular aufgebaute Plattformlösungen, welche individuelle IT-Kompositionen sowie hybride Cloud-/Edge-Deployments erlauben.
Projekt eines App-Stores für die Industrie erhält Community-Label
Bestandsanlagen ins IoT bringen
elektro AUTOMATION: Gibt es Tipps, wie man speziell Bestandsanlagen ins IoT bringt?
Dunkel: In älteren Umgebungen bietet sich der Retrofit-Ansatz an, so dass durch den Einsatz von zum Beispiel Sensorik Metriken erfasst und übermittelt werden können. Bei Umgebungen, die bereits kommunikationsfähig sind, gilt es, die unterschiedlichen Daten und Protokolle inhaltlich zusammen zu bringen. Dies kann durch neue Hardware- oder Software-Komponenten erreicht werden, welche in der Lage sind, die Informationsvielfalt zu harmonisieren und damit die semantische Basis für unternehmensspezifische Prozesse und Anforderungen zu stärken.
Yigitdoel: Es gibt viele Wege, die zum gewünschten Ziel führen. Das macht die Digitalisierung so spannend für Unternehmen, aber auch komplex. Es geht bei solch einer Fragestellung vor allem darum, die vorhandene System- und Datenarchitektur im Blick zu behalten und für diese geplante Erweiterung vorhandene Lösungen – und zwar auf Seiten der Hard- und der Software – zu identifizieren, sowie mit dem Vorhandenen effizient zu kombinieren. Oder anders gesagt: Die Hauptstraße ist im Brownfield-Ansatz in irgendeiner Form vorgegeben und muss berücksichtigt werden. Sobald jetzt die Reiseroute und das Reisemobil gewählt werden, ist es wichtig zu wissen, worauf es dem Betreiber ankommt. Um bei diesem Bild der Reise zu bleiben: Will ich eine schnelle Reise mit wenigen Insassen, beispielsweise um eine Vorstudie oder Machbarkeit in Form eines Proof of Concept zu erreichen, dann ist das Reisemobil eher ein Zweisitzer und der Betreiber fährt mit dem Hersteller der Maschine das Ziel an. Ist ein größerer Umbau geplant – sprich das Ziel definiert –, dann sollte von Beginn an eine Crew eingesetzt werden. Die Zwischenziele der Reise sind so zu wählen, dass diese schnell und effizient erreichbar sind. Um das volle Potential auszuschöpfen, empfiehlt es sich, zunächst die Reiseplanung im Team ganzheitlich durchzuführen. Genau hier sehe ich einen großen Mehrwert und Vorteile einer neutralen Umsetzungsorganisation, wie es die Open Industry 4.0 Alliance ist. Sie bringt alle Disziplinen innerhalb der Technik und auch Industriewissen mit. So wird ein ganzheitlicher Ansatz aufgrund der Diversität der Mitglieder möglich, indem alle relevanten Player im Maschinenbau, in der Softwareindustrie sowie auch als IT-und Systemintegratoren tagtäglich gemeinsam aktiv sind.
Rösinger: Die digitale Anbindung sämtlicher Maschinen in einer Fertigungslogistik ist die Basis für eine erfolgreiche digitale Transformation in Unternehmen. Daher sollte jeder Maschinentyp, unabhängig von Hersteller, Typus und Jahrgang, digital abbildbar sein. Es gibt im Wesentlichen zwei Wege, Anlagen digital anzubinden:
- Bei Maschinen mit netzwerkfähiger Steuerung erfolgt die Anbindung über herstellerspezifische IoT-Softwareadapter – also Plugins, die entweder verfügbar oder individuell zu programmieren sind. Lösungen der OI4-Mitglieder bieten zudem weitere wichtige Komponenten wie ein Maschinen-Repository, also eine Bibliothek von Plugins für alle gängigen, Maschinenhersteller-spezifischen Protokolle, sowie Schnittstellen für alle gängigen Kommunikationsstandards an.
- Bei Maschinen, die nicht für eine Netzwerkkommunikation ausgestattet sind, werden separate Hardware-I/O-Controller an der Maschine positioniert. Diese Edge Devices sollten in der Lage sein, alle Leistungs- und Ressourcen-Daten auszuwerten, welche ihnen Sensoren liefern können – Strom, Wasser, Druck, Hübe und so weiter.
Weitere Infos zur Open Industry 4.0 Alliance (OI4)